
MODELISATION
PRÉSENTATION DU SYSTÈME
Notre projet était de modéliser ce turbocompresseur dans son ensemble. Tout d'abord, nous avons conçu chaque pièce individuellement, ensuite il a fallu créer l'assemblage et enfin nous avons décidé de réaliser une simulation pour vous permettre de mieux comprendre le fonctionnement d'un tel système mécanique. Ci-dessous des aperçus des modélisations des pièces, de l'assemblage ainsi qu'un diaporama avec des rendus réalistes et des vidéos de simulation.
Veuillez cliquer sur l'image pour l'agrandir. De même, vous pouvez cliquer sur l'icone pour télécharger le fichier CAO Catia.
Titre XL


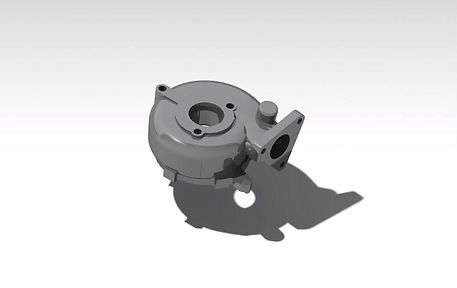

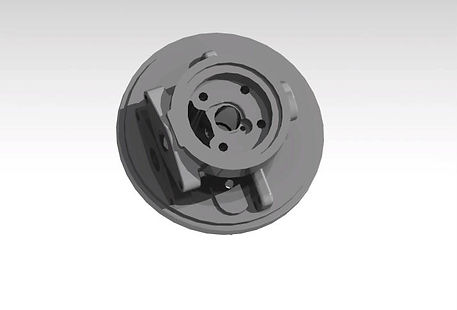
Pièce centrale
Cette pièce est le cœur du turbocompresseur. En effet, toutes les pièces vont venir se fixer et s'articuler autour de celle-ci. Cette pièce a été conçue exclusivement en volumique. Elle peut paraître assez compliquée d'apparence mais en réalité ce ne sont que des formes simple, cela rend la conception plus aisée. Cette pièce est réalisée en fonte, matériau très lourd mais résistant à la chaleur.
Carter gaz d'échappement
Ici, l'une des deux pièces majeures du turbocompresseur. C'est le carter des gaz d'échappement. Il va se fixer sur la pièce centrale et la turbine va se placer à l'intérieur de ce carter. Elle est en fonte car les gaz d'échappement ressortent à très haute température. Cette pièce est sans aucun doute la plus difficile à concevoir de par ses formes. En effet, il a fallu faire une partie en surfacique et une partie en volumique. Le cœur de la pièce a été réalisé en volumique et n'a pas posé trop de problème. La partie la plus dure est celle du contour qui a été établie en surfacique. Pour réaliser cette forme, nous nous sommes appuyés sur une courbe guide en hélice avec variation d'angle et de pas. Une fois ceci réalisé, nous avons effectué un balayage qui permet d'avoir une surface. Ensuite, nous avons extrait cette surface, cherché ses limites et on l'a sur-épaissie. Enfin, on a pu en extraire un volume dans un nouveau corps. Pour finir, nous avons assemblé les deux corps.
Carter gaz d'admission
Le carter des gaz d'admission est la deuxième pièce la plus complexe du projet. Elle vient se fixer aussi sur la pièce centrale mais à l'opposé du carter des gaz d'échappement. Le processus de conception est exactement le même que précédemment. La seule grosse différence est le poids de cette pièce, puisqu'elle est ultra légère. En effet, elle est en aluminium. La turbine d'admission se trouve à l'intérieur de ce carter. L'aluminium peut être utilisé puisqu'il n'y a que les gaz d'admission qui pénètrent dans ce carter, autrement dit de l'air à température extérieure.
Turbine de refoulement et d'admission
Ci-dessus les deux turbines : échappement et admission respectivement en fonte et en aluminium. Ces deux turbines sont reliées aux même axe. Comme dit précédemment, la turbine d'échappement est entraînée par les gaz sortants du moteur et elle entraîne la turbine d'admission qui fait rentrer de l'air dans le moteur. D'un point de vue conception, elles ont été conçues en surfacique à l'aide de courbe sur des plans circulaires. Ensuite, nous avons rempli l'espace entre les plans à l'aide des courbes guides. Ceci nous a permis de réaliser une pale de la turbine. Ensuite, il y a juste à répéter circulairement ces tâches pour obtenir toutes les pales. Une fois ceci réalisé, nous avons extrait les surfaces et cherché les limites. Enfin, on a assemblé les différentes pales et on a créé un nouveau corps dans lequel nous avons transformé les surfaces en volumes. On peut penser que ces pièces sont compliquées à réaliser, mais cela reste faisable et moins difficile que les carters.
Assemblage final du turbocompresseur
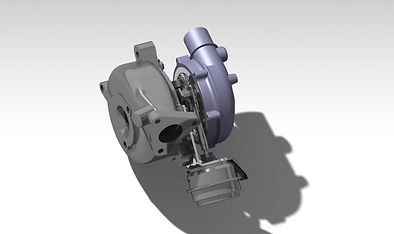

Voici l'assemblage final du turbocompresseur sous deux angles différents. Nous sommes très satisfaits du résultat puisqu'on est très proche de la pièce d'origine. Pour réaliser l'assemblage, il suffit d'utiliser la fonction assemblage de Catia et assembler toutes les pièces conçues séparément en appliquant les contraintes nécessaires. Les différentes couleurs sont dues aux types de matériaux utilisés. Ci-dessous un fichier de l'assemblage et de toutes les pièces, vous pouvez le télécharger et ouvrir le fichier "Assemblage.CATproduct" sous Catia. Cependant, vous devez enregistrer les pièces et l'assemblage dans le même répertoire.
Vue en coupe


METHODE
Problèmes soulevés
Ce projet nous a permis de faire face à de nombreuses difficultés dues à la modélisation de système mécanique. En effet, nous avons rencontré quelques problèmes lors de ce projet. Voici les différents problèmes et les solutions mises en œuvre.
​
-Méthodologie de mesure
-Assemblage
-Modélisation surfacique
Prises de dimensions
1. Pied à coulisse
Pour l'ensemble des pièces, nous avons réalisé la prise de dimensions à l'aide d'un pied à coulisse. Cet instrument permet de mesurer des pièces de trois façons : dimension extérieure (figure 1), dimension intérieure (figure 2) et profondeur (figure 3).
2. Limitations du pied à coulisse
Lors de la modélisation de toutes les pièces avec des surfaces arrondies telles que : les carters, les turbines ... nous avons été confronté à la difficulté de mise en place d'une prise de dimension. Ces pièces donnant une priorité à leur aspect visuel, elles contiennent des formes très difficiles à modéliser. Il est donc très difficile et imprécis d'effectuer la prise de dimensions avec un pied à coulisse.

Assemblage
L'assemblage est l'une des étapes qui nous a posé le plus de problème. En effet, les pièces ont été conçues séparément. Cependant, lors de l'assemblage, toutes les pièces doivent coïncider parfaitement. Ce problème est bien évidemment une conséquence de la prise de mesure. Pour pallier à ce problème, nous nous sommes basés sur la pièce centrale et nous avons tout assemblé autour d'elle. Ensuite, lorsqu'il y avait un petit décalage de trou, on le projetait sur la pièce fixe et on le refaisait. Ces petits ajustements sont souvent très minimes 0.5 mm. Ce ne sont que des ajustements dus aux approximations de mesure. Comme dit précédemment nous nous sommes basés sur une pièce fixe pour réaliser l'assemblage, mais on aurait pu procéder d'une façon différente. La création d'un squelette aurait peut être pu nous faciliter la tâche de l'assemblage. L'assemblage était très important puisque nous voulions réaliser une simulation du système en mouvement (visible dans le diaporama). La simulation fonctionnant cela prouve que notre assemblage ne génère pas d'interférence entre les pièces.
Modélisation surfacique
Le troisième et dernier point qui nous a posé le plus de problèmes est la modélisation surfacique. En effet, ce type de modélisation est beaucoup plus complexe que le modélisation géométrique. Il est très difficile de placer exactement les points au bon endroit dans l'espace et de reproduire les courbes et surfaces parfaitement identiques à la réalité. Nous avons donc essayé de se rapprocher au maximum de la réalité en essayant de faire très attention à nos modélisations dans l'espace. On peut noter que c'est plutôt une réussite puisque les résultats sont très bons. Une fois les surfaces créées, il a fallu en faire des volumes et là aussi ce n'était pas simple. Lorsque les surfaces ont été transformées en volume, nous avons assemblé les corps entre eux pour obtenir qu'une seule et unique pièce.
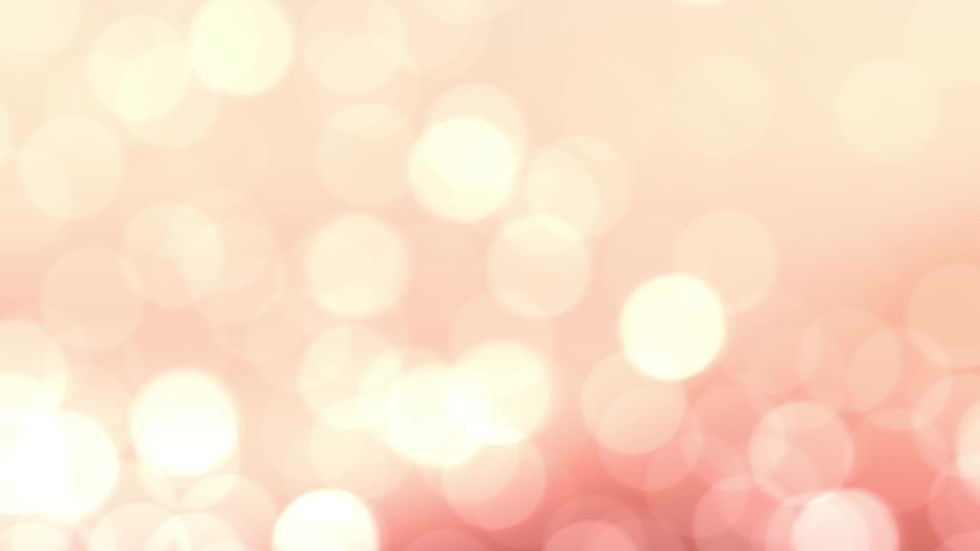
CONCLUSION
Ce projet de l'Unité de Valeur TN20 consistait à modéliser un système mécanique déjà fabriqué à l'aide d'un logiciel de CAO (Conception Assistée par Ordinateur). On appelle cela de la rétro modélisation ou rétro-engineering en anglais. Au cours du semestre, nous avons acquis les bonnes pratiques nous permettant de réaliser des modélisations cohérentes que ce soit en surfacique ou en volumique.
Ce projet nous a permis d'être confrontés aux problématiques rencontrées lors de la phase de modélisation (notamment en surfacique) sans prendre en compte la phase de conception en amont (résistance des matériaux...)
​
Ce travail réalisé en binôme est une réussite malgré la difficulté du sujet qui était assez élevée. Nous sommes donc très satisfait du travail accompli et surtout du résultat obtenu.
​
Pour finir, nous souhaitons remercier Mohamed Othman-Latrous pour ses conseils et le suivi du projet.
​
Si vous avez des questions sur ce projet n'hésitez pas à nous contacter.
Modélisation d'un Turbocompresseur

PRODUIT
AUTOMOBILE
SURALIMENTATION
ECONOMIQUE
Les moteurs équipés de turbocompresseur ont une consommation inférieure aux moteurs atmosphériques
Suralimente le moteur en air ce qui permet d'avoir plus de puissance
Application dans le domaine automobile
INTRODUCTION
Le système que nous avons décidé de modéliser est un turbocompresseur de Volkswagen Passat 1L9 TDI. Ce système mécanique convient tout à fait aux attentes du projet puisqu'il contient des pièces complexes comme les hélices, des pièces surfaciques comme les carters et un certain nombre de pièces pour satisfaire le cahier des charges du projet TN20.
FONCTION
Le turbocompresseur sert à suralimenter le moteur en air. Il est composé de deux hélices ; la première est entraînée par les gaz d'échappement, et elle entraîne la seconde. La deuxième hélice a pour but de faire rentrer de l'air dans le moteur. De plus, entre les deux hélices, des ailettes amovibles sont présentes et permettent de gérer la soupape de surpression. D'où le nom de turbocompresseur. La plupart des voitures sont équipées de ce système. Les véhicules très haut de gamme peuvent avoir jusqu'à quatre turbocompresseurs car le gain de puissance avec ce système mécanique est très important.